New Warner Lambert chewing gum brand sparkles in holographic package
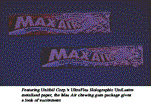
Wrapped in award-winning packaging, Max Air, Warner Lambert's new sugarless, vapor-action chewing gum brand, has "exceeded the company's sales expectations by 60%." That's according to Graham Kaufman, senior brand manager, Warner Lambert Canada Inc., who says that the metalized package sets a "new gold standard in packaging."
The pellet-shaped gum delivers what Warner Lambert calls "the personal exhilaration consumers are looking for." The company wanted packaging that would tout the product's ability to give users a blast of vapor when they bite into it.
Creating a package that would have "high impact and not be just another pack of gum on the shelf was key," says Russell Wright, senior research associate at Warner Lambert's headquarters in Morris Plains, NJ. "The package had to really talk about the burst of flavor you get with Max Air."
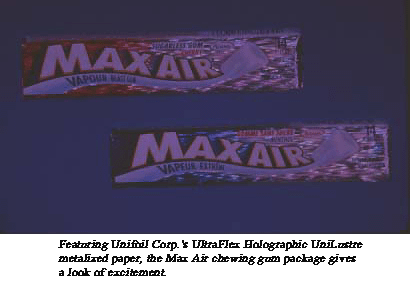
The package was created especially for Warner Lambert by Unifoil Corp. (Passaic Park, NJ). It is made with Unifoil's UltraFlex Holographic UniLustre, a non-laminated, multi-dimensional metalized paper that adds depth and movement to printed materials and packaging. Crown Roll Leaf (Paterson, NJ) supplied a proprietary holographic film. Branded image company, Davis & Associates, designed the look of the Max Air package, and Ontario-based Lawson Mardon Flexible converted and printed it.
Exciting gum
Max Air's origins can be traced back to 1998 when Warner Lambert saw a competitor's cough/cold gum encroaching on its popular Hall's franchise. The company learned that consumers seemed more interested in a gum that was exciting and exhilarating rather than one that offered cough relief.
"We did not want to cannibalize the Hall's market, which is strongly established," says Kaufman. "And it was clear consumers were interested in an exciting new product. So we built a strong new brand that has a high flavor profile and positioned in an optimal way."
Adds Wright, "Overcrowding on the shelf is a problem. Marketing was adamant about asking for an upgraded package that was distinctive."
"Initially we tried a microembossed paper," says Wright, who along with his associates researched shelf-impact technologies prior to the company's decision to build the new Max Air brand. "But the problem with that technology was that little pieces of foil popped off the paper."
Enter Unifoil Corp. "We wanted a flexible holographic material that could be effectively overprinted, laminated with a foil high barrier, have excellent deadfold properties and accept seal coatings. And there could be absolutely no flaking," explains Wright. It's a tall order, but Wright says Ultraflex Holographic UniLustre was able to meet it.
Feeling of ‘movement'
To create the right look for Max Air, Warner Lambert called upon Davis & Associates. Lawrence Dadds, design director at Davis & Associates, notes that because Max Air gives those who bite into it a blast of vapor, the package had to convey excitement and differentiation. "And we wanted to capture a feeling of movement, like the vapor action," he adds.
After reviewing a number of holographic samples that weren't quite right, Davis & Associates was introduced by package-maker Lawson Mardon Flexible to Unifoil's Ultraflex Holographic UniLustre made with Crown Roll Leaf holographic film.
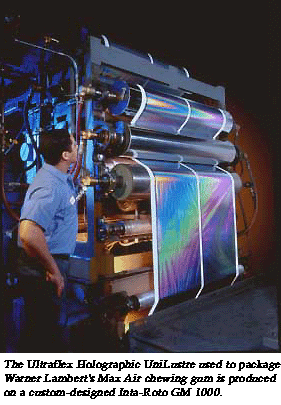
Dadds, who specializes in design on small packages, built prototypes in order to experiment with the graphic elements. Warner Lambert wanted to let the holography shine through, rather than clutter the package with an abundance of brand name and benefits statements. Dadds accomplished this by selecting opaque and transparent inks for the six-color job.
Printing coup
The final package was made with Ultraflex Holographic UniLustre on 25# paper that was laminated on the reverse side with aluminum foil for barrier properties and freshness. It was printed by Lawson Mardon Flexible, which ran the job in one pass on an eight-station Cerutti gravure press.
"The quality of the printing was a real coup," says Wright. "The tight registration and transparent inks enabled us to get exact positioning of the graphics and maintain the high impact of the holography."
The Ultraflex also enabled high-speed package wrapping. "This was critical for achieving good crisp folds and good tack for the inner seal," contends Wright.
The Max Air package received a 1999 Gold Award in packaging design from the Packaging Association in Canada. Additionally, it received the Association for Industrial Metallizers, Coaters and Laminators' AIMCAL 2000 Metallized or Vacuum Coated Package and Label competition technical achievements in the food category (see related article).
Max Air is currently sold in Canada, Portugal, Japan and Mexico. Rollouts in other countries are pending.
For more information:
Unifoil Corp. (Passaic Park, NJ), Tel: 973-365-2000, Fax: 973-365-0924
Crown Roll Leaf (Paterson, NJ), Tel: 973-742-4000, Fax: 973-742-0219
Lawson Mardon Flexible (Mississauga, Ontario), Tel: 905-821-9711, Fax: 905-821-1457
Edited by Bill Noone